People would know you from Racers Edge, but you’re a big part of the McMartin Racing Team which has just taken delivery of the new Ducati V4 R. Tell us what happens when a new model turns up.
In this case, we were lucky to get a hold of a set of Aruba panels from the Ducati WorldSBK team in February, but we can’t take moulds off those panels – they are different – but we can get a guide and see how they’ve gone about the process, where they’ve joined panels, things like that. Then we make what we call a set of plugs, really heavy replicas from the bodywork.
We just make sure everything fits together. From those plugs we make a set of moulds, and the moulds are the tool we use to make our race panels.
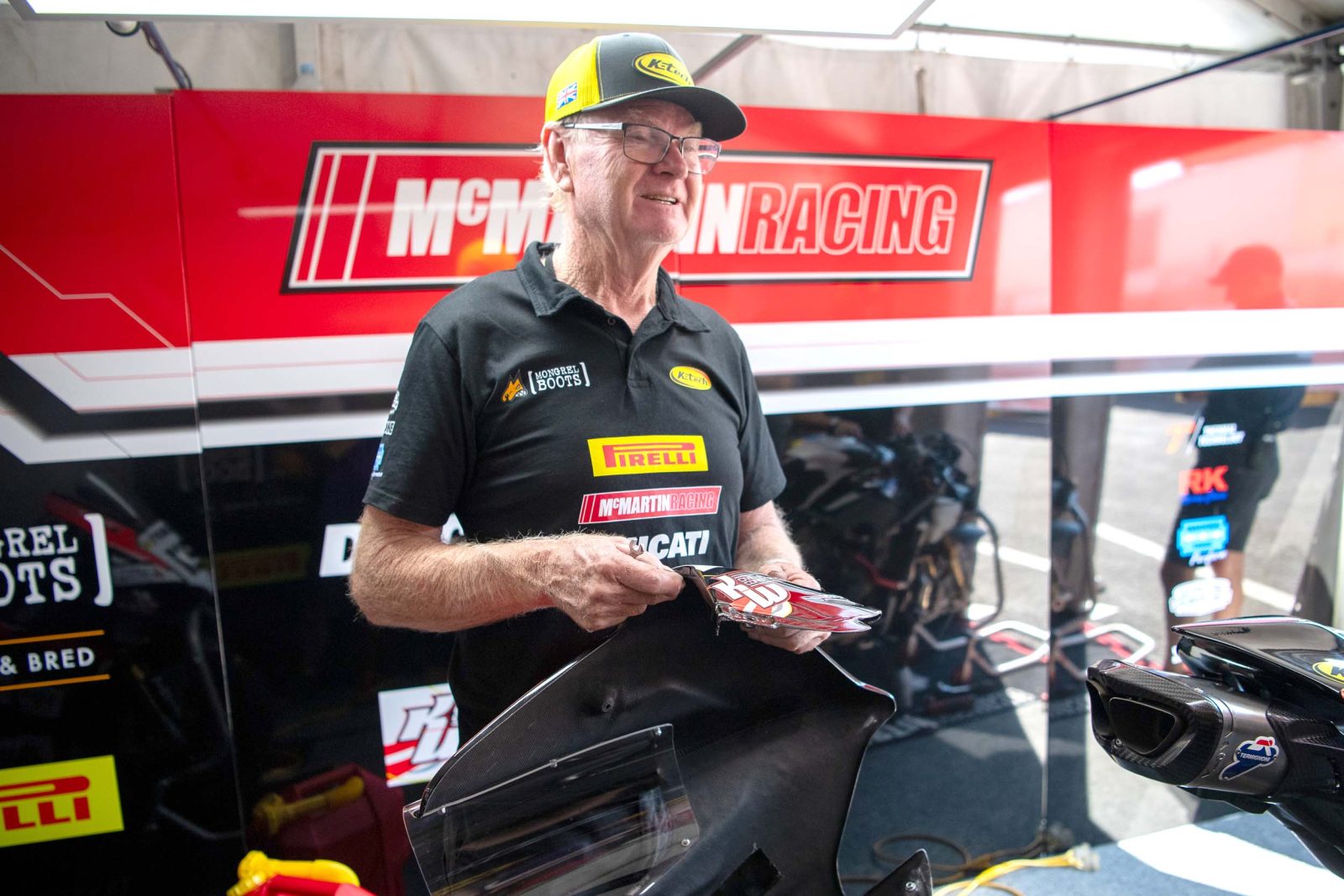
Are the plugs plastic or fibreglass?
The plugs are fibreglass and are three or four millimetres thick. They are stable and don’t distort. The moulds are also quite thick, about five millimetres, and they have a special surface on them. The panels we have here for McMartin Racing are all carbon-fibre, but most of our customer panels are fibreglass.
What’s involved in the process of making a panel?
It’s like making a cake. The mould is prepared with a release agent and then waxed up. Firstly, we put a gel coat down so it makes it easier for painting – the whole process happens in reverse. Then we use a resin and dry carbon-fibre mix. We lay the fibre down and wet it out with a liquid resin. There are other ways of doing it – but they are very expensive. Fairings are disposable items, as long as they are light, that’s the most important thing.
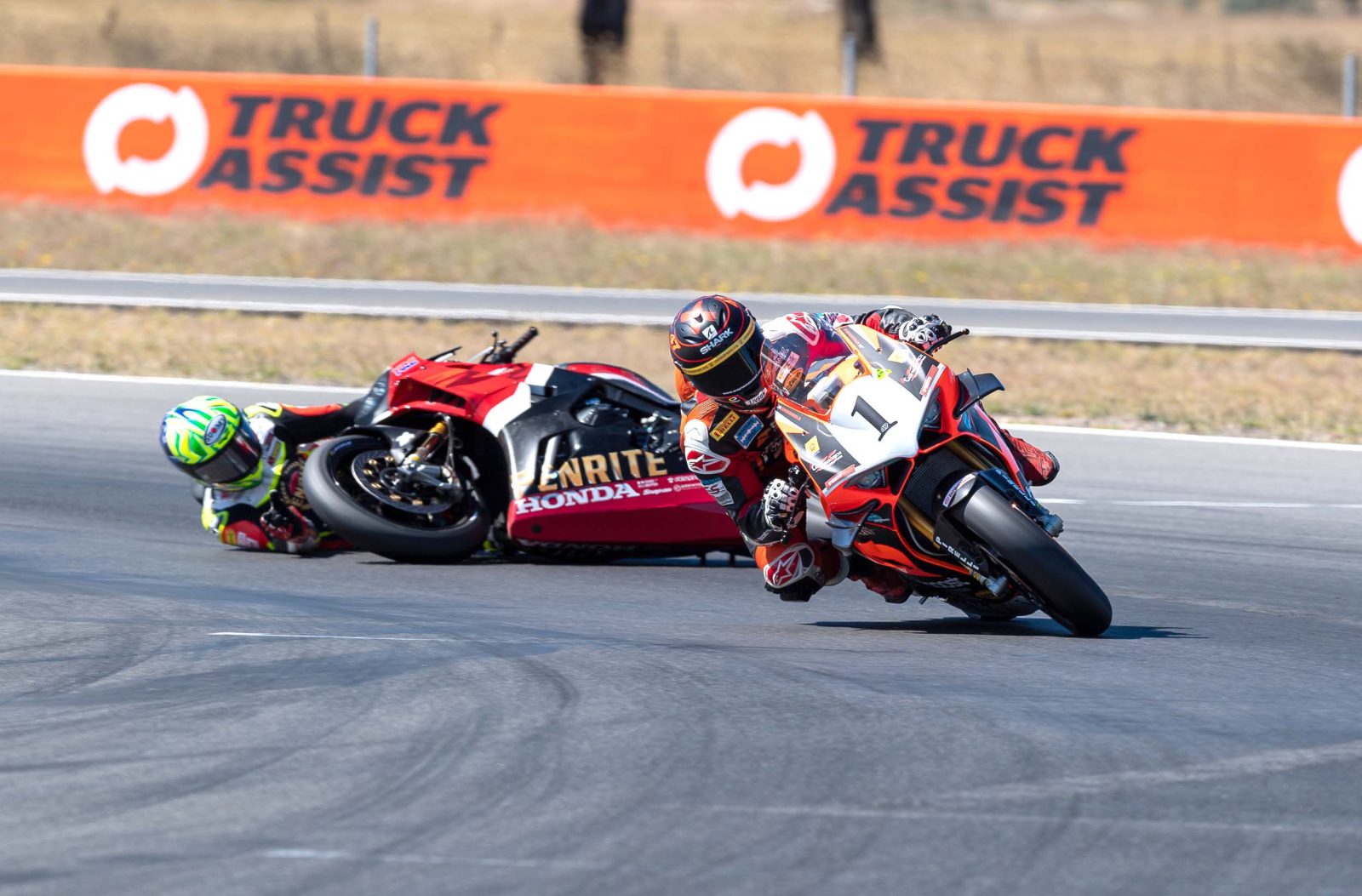
You said the panels for the Ducati are backwards compatible – the new panels fit the old bike, but not the other way around. Where did you start on the 2023 V4 R?
If we start from the nose, it primarily looks very similar. The actual air intake tube is now part of the fairing itself, not a tube that sits onto the motorbike. That’s one of the things we copied off the WorldSBK team.
The side panels have three or four extra vents on the side – they’re not just cuts, they are pods that create a venturi effect. They’ve been copied exactly from the roadbike – obviously, the bikes don’t run as hot as a roadbike so this has really helped out.

The bellypan can’t be copied though. How does that work out?
Because of the exhaust systems with the V4 configuration, the bellypan tends to be very wide – so we need to get it pulled into the motorbike as much as we can so it doesn’t scrape on the ground. We’ve seen from our data that Josh (Waters), and Wayne (Maxwell) before him, they will get up to 63 degrees of lean angle and the belly pans can touch on the ground if you’re not careful.
We looked at what the WorldSBK guys have done and then modified our design to suit our exhaust system. They don’t have the noise restrictions we have, so they have different pipes. To get the length of the exhaust system correct there is a lot of plumbing underneath the bellypan that has to run close to the bodywork and engine.
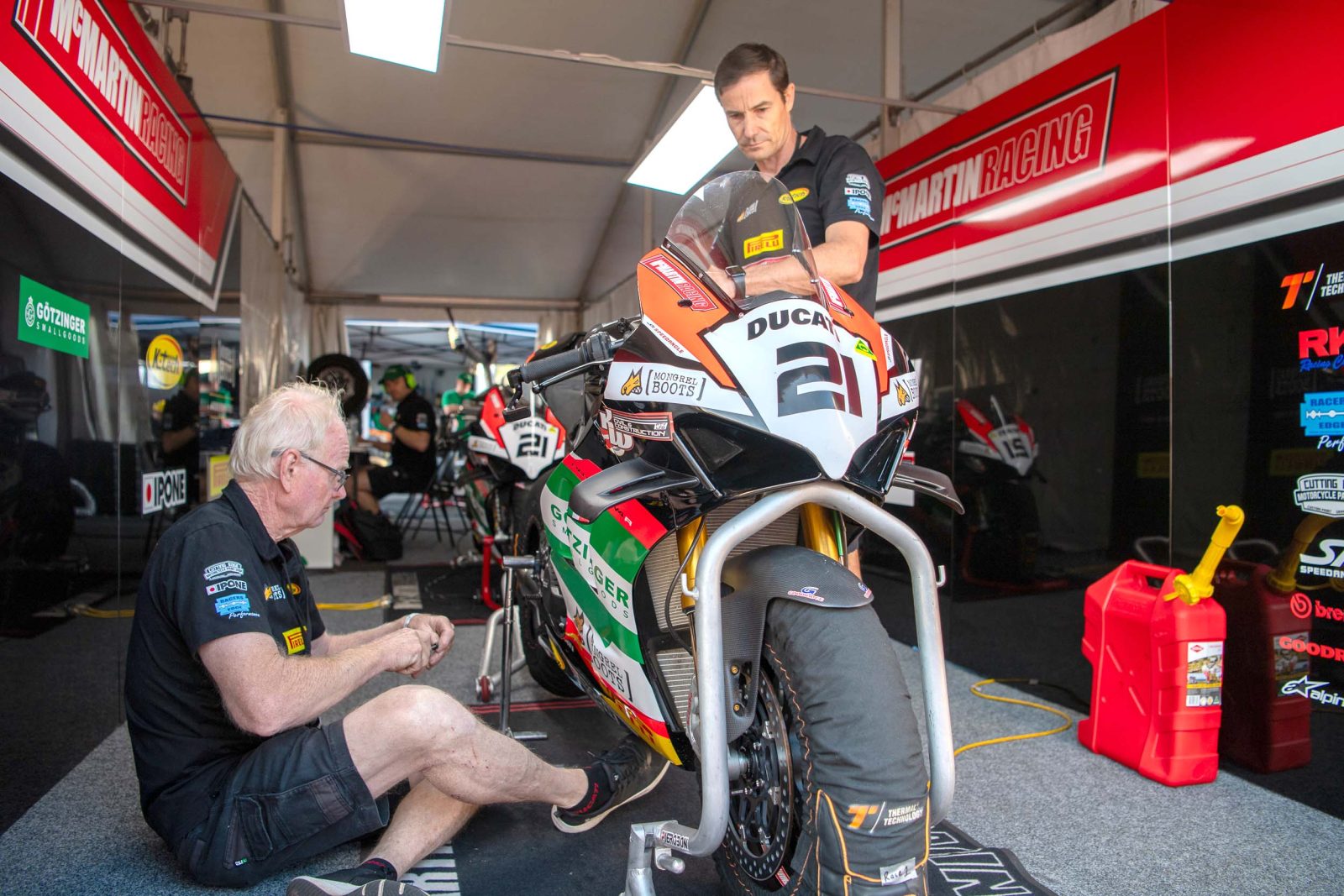
What sort of costs are we talking about to get a new set of moulds ready for production?
We’re looking at about $25k in the set-up and tooling. When we choose to make panels for a new motorbike, we’ve got to look at what sales are going to be like. For example, we’d love to do the Honda but there is only one guy on the grid riding it – there also aren’t many at trackdays.
We do all the Yamaha panels for the factory Superbike team, and that filters all the way down to trackday riders. When a new model comes out we will often get them a few months before the world release so we can get a headstart. We generally work straight from the roadbike panels. It’s time-consuming, a lot of sitting around and looking at the bike, doing sketches. These days we do a little bit of 3D modelling. We’ve invested in a scanner and printer, which moves us into the 21st century.
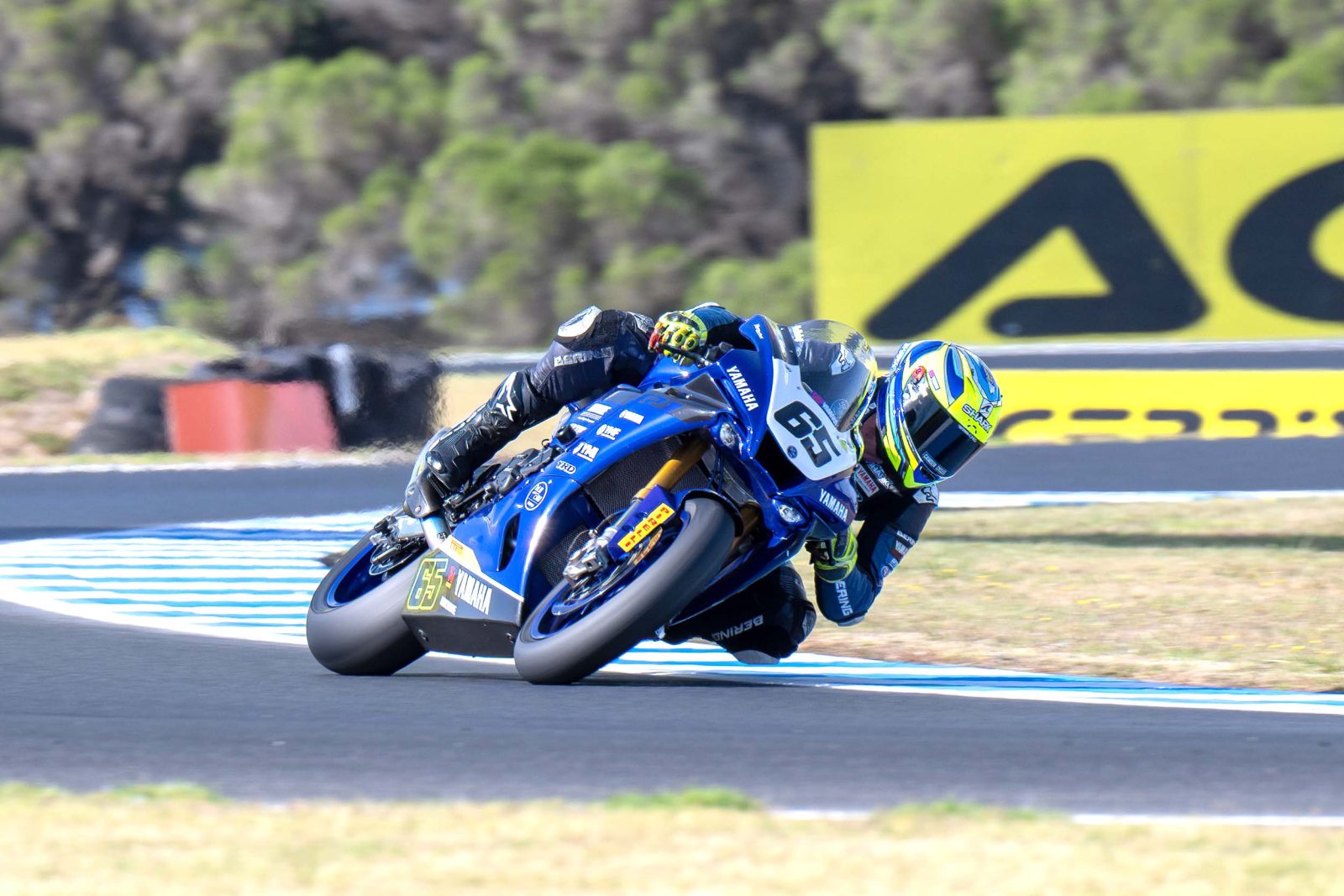
Why would you choose carbon-fibre over fibreglass?
We use carbon for the stiffness – there’s not a lot of difference in weight. The actual stiffness of the panel will resist bending more, which is important at Superbike speeds. We don’t want to see any distortion in the panel.
What about the wings? They were a talking point in regard to expense when they first appeared.
They are a mix of plastic and carbon; practicality wins out here. The wings are often the first thing to hit the deck in a crash. Also, the fuel tank is worth $4500, so we design a custom protector for that which I mould directly off the tank. We’ve also got a tank extender, which is a comfort thing for Josh, as well as a fully customised seat.
Words Matt O’Connell + Photography Rob Mott & Racers Edge